CAE于發(fā)動機蓋拓撲優(yōu)化中的應(yīng)用
2017-01-05 by:CAE仿真在線 來源:互聯(lián)網(wǎng)
1 前言
發(fā)動機蓋是車身中的關(guān)鍵部件,其性能直接影響了汽車的NVH性能、碰撞安全性能、防水性、門蓋開啟方便性及整車外觀等。因此,對汽車發(fā)動機蓋的模態(tài),剛度、強度進行分析研究及優(yōu)化顯得很有必要。
本文通過有限元分析方法,利用HyperMesh建立有限元分析模型,采用OptiStruct求解器進行計算求解。通過分析結(jié)果對比,對不合格工況進行拓撲優(yōu)化,并對最終優(yōu)化后的結(jié)果進行性能檢驗。
2 模型概況
發(fā)動機蓋總成以鈑金件為主,在結(jié)構(gòu)上一般由外板和內(nèi)板組成,中間夾以隔熱材料,內(nèi)板起到增強剛性的作用,該總成還包括鎖鉤加強板,鎖鉤,鉸鏈,鉸鏈支座,鉸鏈加強板。
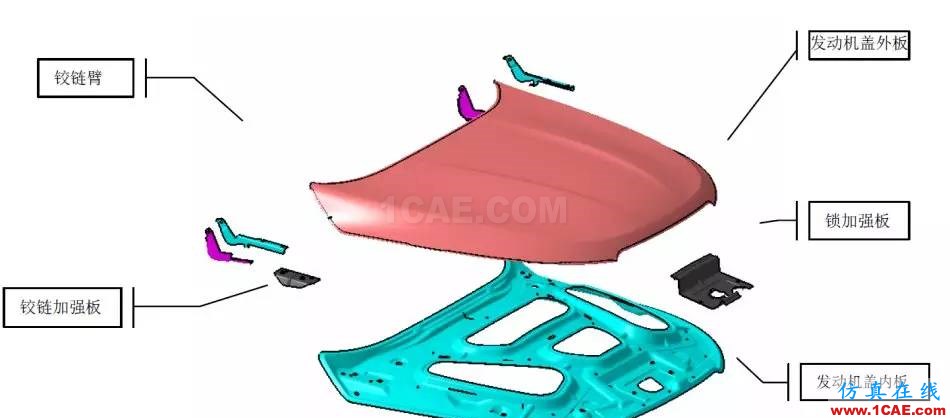
圖1.1發(fā)動機蓋有限元模型
有限元模型主要采用殼單元和實體單元進行建模:其中內(nèi)板,外板,鎖加強板,鉸鏈,鉸鏈支座,鉸鏈加強板按10mm進行網(wǎng)格劃分,殼單元總共34427個,鎖鉤劃分為實體單元,因為鎖鉤尺寸比較小,按照3mm進行網(wǎng)格劃分。發(fā)動機蓋內(nèi)外板的邊緣通過包邊處理實現(xiàn)連接;鉸鏈固定在車身上,采用RBE2模擬螺栓連接,并約束六自由度使其固定;鉸鏈座與鉸鏈臂之間采用銷軸連接,通過RBE2模擬螺栓連接,約束12346自由度,放開Y軸的旋轉(zhuǎn)自由度5;鉸鏈與內(nèi)板的連接采用螺栓,通過RBE2單元進行模擬,約束123456自由度;內(nèi)板與外板之間的膠連接,通過ACM單元模擬實現(xiàn);鉸鏈處的焊點采用CWELD單元模擬實現(xiàn);鎖鉤與鎖加強板之間是焊接關(guān)系,鎖鉤是體單元,為了更真實的模擬連接關(guān)系采用RBE2單元模擬實現(xiàn);緩沖塊采用彈簧SPRING單元實現(xiàn),密封膠采用CBUSH單元模擬實現(xiàn)。發(fā)動機蓋總成質(zhì)量為17.48kg,模型的材料屬性見表1.1,其中發(fā)動機蓋總成結(jié)構(gòu)有限元模型如圖1.1所示。
表1.1 模型材料屬性

3 模型分析
3.1模型計算及分析結(jié)果
模型檢查無誤之后,進行工況加載并計算。發(fā)動機蓋的模型計算工況包括剛度、強度、模態(tài)、非線性分析等等十多種,讀取計算結(jié)果與工況要求目標(biāo)值進行比較:自由模態(tài)工況中的扭轉(zhuǎn)模態(tài)為24.59HZ,小于合格目標(biāo)值30HZ,不滿足工況要求;扭轉(zhuǎn)剛度為8750.70N·m/rad,略小于合格目標(biāo)值9000N·m/rad,不滿足工況要求;前乘坐工況的最大應(yīng)力為183.19MPa,大于屈服應(yīng)力,不滿足工況要求;側(cè)乘坐工況的最大應(yīng)力為171.99MPa,與屈服應(yīng)力非常接近;后乘坐工況的最大應(yīng)力為209.39 MPa,大于屈服應(yīng)力,不滿足工況要求。
綜上所述,自由模態(tài)的扭轉(zhuǎn)模態(tài)、扭轉(zhuǎn)剛度、乘坐(前乘坐、側(cè)乘坐、后乘坐)強度、下拉強度等等工況的計算結(jié)果,不滿足設(shè)計工況要求,需要進行結(jié)構(gòu)優(yōu)化。
3.2發(fā)動機蓋內(nèi)板結(jié)構(gòu)優(yōu)化分析
拓撲優(yōu)化的研究領(lǐng)域主要分為連續(xù)體拓撲優(yōu)化和離散結(jié)構(gòu)拓撲優(yōu)化。不論哪個領(lǐng)域,都要依賴于有限元方法。連續(xù)體拓撲優(yōu)化是把優(yōu)化空間的材料離散成有限個單元(殼單元或者體單元),離散結(jié)構(gòu)拓撲優(yōu)化是在設(shè)計空間內(nèi)建立一個由有限個梁單元組成的基礎(chǔ)結(jié)構(gòu),然后根據(jù)算法確定設(shè)計空間內(nèi)單元的去留,保留下來的單元即構(gòu)成最終的拓撲方案,從而實現(xiàn)拓撲優(yōu)化。目前,連續(xù)體拓撲優(yōu)化的研究已經(jīng)較為成熟,主要有均勻化方法、變密度法、漸進結(jié)構(gòu)優(yōu)化法(ESO)以及水平集方法等。
由上面分析可知多種工況不滿足設(shè)計要求,需要對發(fā)動機蓋總成進行優(yōu)化改進。對于發(fā)動機蓋總成來說,外板及鉸鏈的形狀一般不可以改變,外板為空間曲面板,要迎合整車造型的需求,體現(xiàn)轎車的外形風(fēng)格,結(jié)構(gòu)優(yōu)化的空間不大。內(nèi)板為薄鋼板,筋條網(wǎng)格狀布置,其主體結(jié)構(gòu)可根據(jù)需要布置孔洞,以減輕自身重量,內(nèi)板的作用還包括:加強結(jié)構(gòu)剛度、達到足夠的抗凹性能及滿足碰撞(行人保護)法規(guī)要求,此外兼顧加工工藝、輕量化、車身的防腐蝕和最低成本原則等方面的需要。
本文在保證發(fā)動機蓋總成外板形狀不變的情況下,采用變密度法對發(fā)動機蓋內(nèi)板及加強件進行拓撲優(yōu)化。因發(fā)動機蓋內(nèi)板結(jié)構(gòu)多種多樣,對發(fā)動機蓋的模態(tài)、剛度和其他性能的影響較大,這里僅考察內(nèi)板結(jié)構(gòu)優(yōu)化設(shè)計對發(fā)動機蓋總成模態(tài)、剛度和強度的性能提升影響。
優(yōu)化分析步驟:
1) 設(shè)定約束
優(yōu)化約束是在優(yōu)化過程中必須滿足的條件,為了保持發(fā)動機蓋的性能,故需要約束。權(quán)衡計算速度,本文選取發(fā)動機蓋自由扭轉(zhuǎn)模態(tài)和扭轉(zhuǎn)剛度作為優(yōu)化約束,要求各優(yōu)化約束指標(biāo)均不低于原設(shè)計性能。本文中設(shè)定自由扭轉(zhuǎn)模態(tài)固有頻率最小為30HZ,扭轉(zhuǎn)剛度為9000N·m/rad。
2) 設(shè)計變量
OptiStruct的拓撲優(yōu)化過程采用變密度法。該方法假設(shè)材料的彈性模量與材料的密度為確定的數(shù)學(xué)關(guān)系,且每個設(shè)計單元的密度為一個優(yōu)化變量。當(dāng)優(yōu)化結(jié)果表示設(shè)計單元的密度接近0,表示該單元彈性模量接近0,即該單元對考察的優(yōu)化工況沒有貢獻,該單元應(yīng)剔除;若密度越接近1,表示該單元的貢獻量越大,該單元需要優(yōu)先保留。在本文中因為內(nèi)板的厚度為0.7mm,設(shè)置basethickness =0.7mm,內(nèi)板的厚度在0.7-1.5mm之間變化。
3) 優(yōu)化結(jié)果分析
通過HyperView進行后處理,并查看優(yōu)化結(jié)果。設(shè)計單元的密度是該內(nèi)板結(jié)構(gòu)保留或增強的標(biāo)志。密度越高,顏色越紅,則說明該結(jié)構(gòu)對所考察的工況越重要,反之,密度越低,顏色接近藍色,則該結(jié)構(gòu)對所考察的工況所起的作用越小。從密度分布圖2.1中可以看出:內(nèi)板的”A”字肋比較薄弱,需要進行加強改善以提高發(fā)動機蓋總成的性能。

圖2.1拓撲優(yōu)化結(jié)果-內(nèi)板密度效果圖
3.3 優(yōu)化方案
1)根據(jù)工藝要求,對于易引起大變動的結(jié)構(gòu)部位或者是與其他總成的連接部位盡量維持原有設(shè)計,減少模具的改造成本,紅黃藍三線框圖所示,例如:裝焊安裝孔,緩沖臺,鎖扣安裝位置等等,見圖2.2,對于這些部位稍有變動,會引起其他連接件的變動,涉及范圍比較廣,增加了經(jīng)濟成本,所以這些部位都維持原有的設(shè)計。
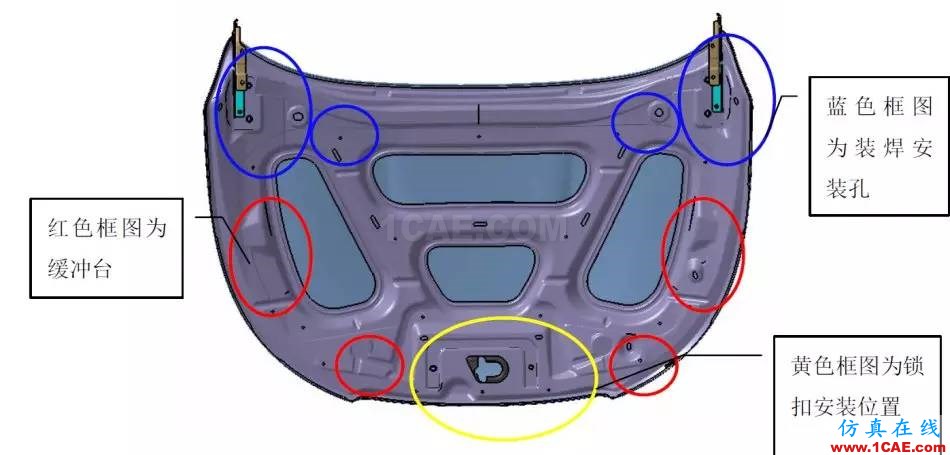
圖2.2幾何模型
2) 根據(jù)經(jīng)驗并參考優(yōu)化結(jié)果,提出了兩種改進方案:
方案一修改”A”字形的中間肋的結(jié)構(gòu),增加截面面積,增大垂向的傾斜度,見圖2.3。
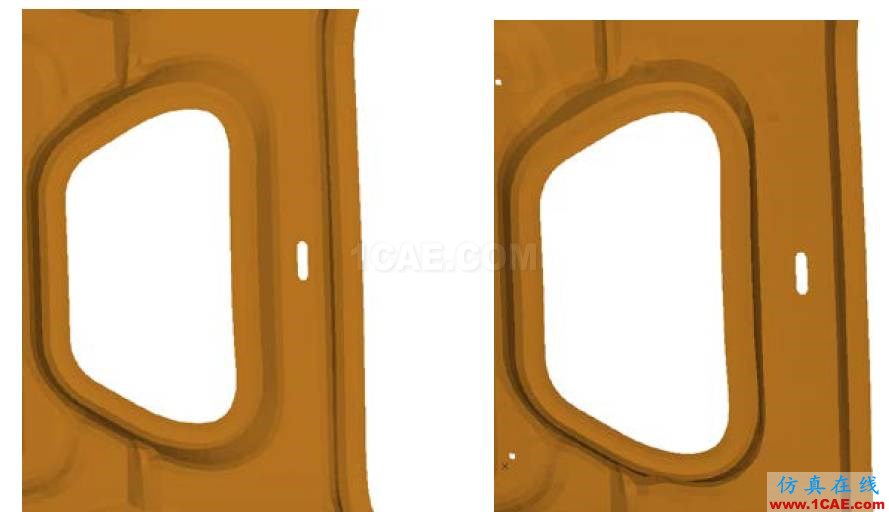
圖2.3 方案一
方案一的計算結(jié)果:自由模態(tài)工況中的扭轉(zhuǎn)模態(tài)為26.34HZ,小于合格目標(biāo)值,不滿足工況要求;扭轉(zhuǎn)剛度為9260N·m/rad,略大于合格目標(biāo)值,滿足工況要求;前乘坐工況的最大應(yīng)力為195.23MPa,大于屈服應(yīng)力,不滿足工況要求;側(cè)乘坐工況的最大應(yīng)力為107.43MPa,小于屈服應(yīng)力,滿足工況要求;后乘坐工況的最大應(yīng)力為88.45MPa,小于屈服應(yīng)力,滿足工況要求。
方案二抬高如圖2.4所示的兩個部位,使“A”字形內(nèi)板結(jié)構(gòu)更加完整。
方案二的計算結(jié)果:自由模態(tài)工況中的扭轉(zhuǎn)模態(tài)為30.04HZ,略大于合格目標(biāo)值,滿足工況要求;扭轉(zhuǎn)剛度為11771.30N·m/rad,大于合格目標(biāo)值,滿足工況要求;前乘坐工況的最大應(yīng)力為182.11MPa,略微大于材料承受的最大屈服應(yīng)力,不滿足工況要求;側(cè)乘坐工況的最大應(yīng)力為101.21MPa,小于屈服應(yīng)力,滿足工況要求;后乘坐工況的最大應(yīng)力為86.42MPa,小于屈服應(yīng)力,滿足工況要求。
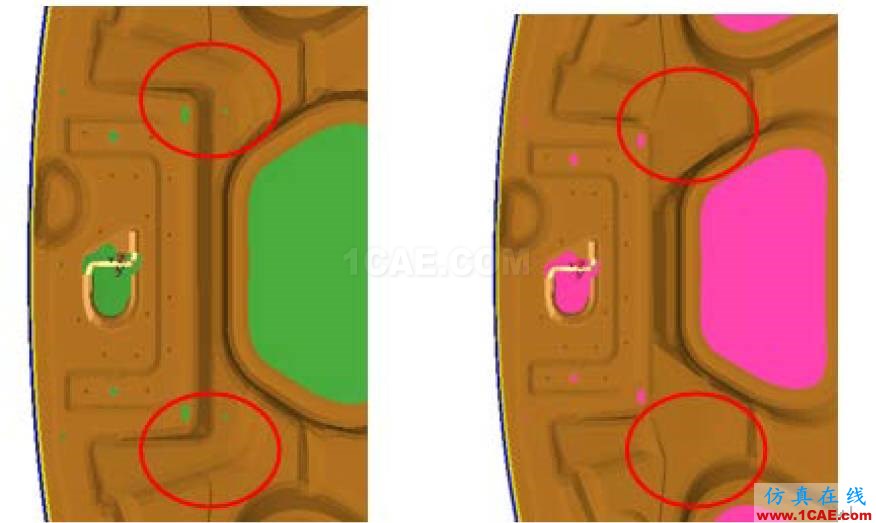
圖2.4 方案二
綜上所述,自由扭轉(zhuǎn)模態(tài)均滿足設(shè)計要求,前乘坐應(yīng)力略大于目標(biāo)值,而且前乘坐工況只是偶爾會發(fā)生的現(xiàn)象,在計算中也會存在誤差,所以此處忽略前乘坐應(yīng)力稍大的情況,方案二基本上滿足設(shè)計要求。在滿足設(shè)計要求的同時發(fā)動機蓋總成的質(zhì)量也沒有增加,所以本文采用方案二的優(yōu)化設(shè)計方案,至此優(yōu)化結(jié)束。
相關(guān)標(biāo)簽搜索:CAE于發(fā)動機蓋拓撲優(yōu)化中的應(yīng)用 HyperWorks有限元分析培訓(xùn) HyperMesh網(wǎng)格劃分培訓(xùn) hyperMesh視頻教程 HyperWorks學(xué)習(xí)教程 HyperWorks培訓(xùn)教程 HyperWorks資料下載 HyperMesh代做 HyperMesh基礎(chǔ)知識 Fluent、CFX流體分析 HFSS電磁分析 Ansys培訓(xùn) Abaqus培訓(xùn)